NATA's general equipment table: why you shouldn't follow it to a T.
- Quality & Advice
- Mar 31, 2020
- 2 min read
Updated: Feb 19, 2024
One of the most common misconceptions NATA accredited facilities have, is that NATA makes the rules about how you maintain your equipment. The general equipment table used to be treated as gospel and those who transgressed risked a telling-off from the auditor.
A facility manager once told me they wouldn't consider varying calibration frequencies of their equipment because it had been too stressful to have them 'approved' by NATA in the first place.
The accreditation environment has shifted significantly since then. Standards such as ISO 9001, ISO 17025 and ISO 17020 are built on risk-based philosophy. Essentially, it is your responsibility to consider risks and justify how your decisions don't invalidate your results.
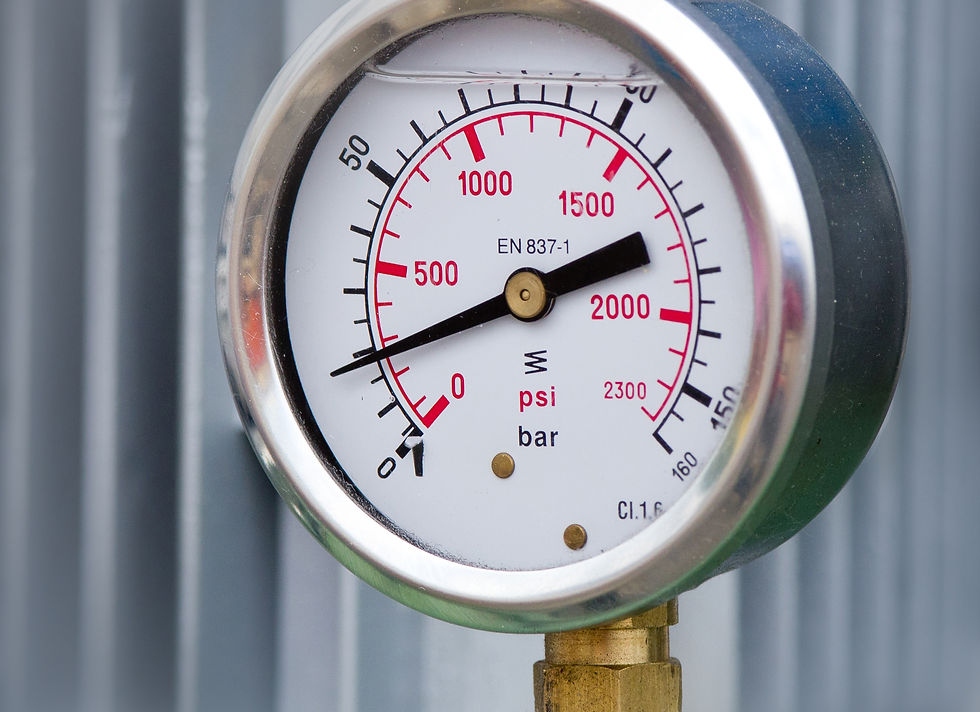
When it comes to your equipment, and how often they should be calibrated or checked, the recommended frequencies are a good starting point. Keep in mind though that NATA's general equipment table provides guidance to a range of industries that use equipment in a variety of applications and environments.
For your equipment maintenance schedule, consider the following:
Measurement uncertainty requirements.

Measurements must be traceable to SI units, but the accuracy required by the measurement may not warrant frequent calibrations. It might be more appropriate, for example, to regularly check the equipment against calibrated reference standards. This might be especially cost effective if you have a high turnover of the particular item of equipment.
Equipment used infrequently.
If you bring out a particular item of equipment only once or twice a year, it may not make sense to send it out for calibration annually. Calibration or a check before use might be a better option.
Equipment exposed to the elements.

Items that get roughly treated, or are exposed to harsh conditions will degrade more rapidly than if they were used in a controlled laboratory. If you are using or storing your equipment in adverse conditions, then it would be wise to be checking they are in good working order more frequently.
Equipment proven to be stable over time.
If you are like most facilities, when you get a calibration certificate you eyeball it and file it away. It might be worth your while to have a good review of the calibration and verification history of your equipment. You may already have really good data to demonstrate that the equipment hasn't needed adjustments over a significant period of time and that reducing the calibration and check frequencies are justifiable.
*Disclaimer* I'm not advocating throwing out your equipment calibration schedule and extending out all calibrations to 10-yearly! Before you make changes, make sure you can appropriately justify that your results are not compromised!
Q&A NATA accreditation consultants can help:
Rationalise your equipment calibration and in-service check schedule based on assessment of risk;
Simplify your equipment check processes and revise your forms for ease of use;
Train your staff in effective equipment check processes, and how to review calibration certificates.
Comments